सेमीकंडक्टर विनिर्माण प्रक्रिया में एक महत्वपूर्ण चरण के रूप में वेफर डाइसिंग प्रौद्योगिकी, चिप प्रदर्शन, उपज और उत्पादन लागत से सीधे जुड़ी हुई है।
#01 वेफर डाइसिंग की पृष्ठभूमि और महत्व
1.1 वेफर डाइसिंग की परिभाषा
वेफर डाइसिंग (जिसे स्क्राइबिंग भी कहते हैं) अर्धचालक निर्माण में एक आवश्यक चरण है, जिसका उद्देश्य प्रसंस्कृत वेफर्स को कई अलग-अलग डाइज़ में विभाजित करना है। इन डाइज़ में आमतौर पर संपूर्ण सर्किट कार्यक्षमता होती है और ये इलेक्ट्रॉनिक उपकरणों के उत्पादन में अंततः उपयोग किए जाने वाले मुख्य घटक होते हैं। जैसे-जैसे चिप डिज़ाइन अधिक जटिल होते जाते हैं और आयाम सिकुड़ते जाते हैं, वेफर डाइसिंग तकनीक के लिए सटीकता और दक्षता की आवश्यकताएँ लगातार कठोर होती जा रही हैं।
व्यावहारिक कार्यों में, वेफर डाइसिंग में आमतौर पर हीरे के ब्लेड जैसे उच्च-सटीक उपकरणों का उपयोग किया जाता है ताकि यह सुनिश्चित किया जा सके कि प्रत्येक डाई बरकरार और पूरी तरह कार्यात्मक रहे। प्रमुख चरणों में काटने से पहले तैयारी, काटने की प्रक्रिया के दौरान सटीक नियंत्रण और काटने के बाद गुणवत्ता निरीक्षण शामिल हैं।
काटने से पहले, सटीक कटिंग पथ सुनिश्चित करने के लिए वेफर को चिह्नित और स्थितिबद्ध किया जाना चाहिए। काटने के दौरान, वेफर को क्षति से बचाने के लिए उपकरण के दबाव और गति जैसे मापदंडों को कड़ाई से नियंत्रित किया जाना चाहिए। काटने के बाद, यह सुनिश्चित करने के लिए व्यापक गुणवत्ता निरीक्षण किया जाता है कि प्रत्येक चिप प्रदर्शन मानकों पर खरी उतरे।
वेफर डाइसिंग तकनीक के मूल सिद्धांतों में न केवल काटने के उपकरण का चयन और प्रक्रिया मापदंडों का निर्धारण शामिल है, बल्कि काटने की गुणवत्ता पर पदार्थों के यांत्रिक गुणों और विशेषताओं का प्रभाव भी शामिल है। उदाहरण के लिए, निम्न-k डाइइलेक्ट्रिक सिलिकॉन वेफर्स, अपने निम्न यांत्रिक गुणों के कारण, काटने के दौरान तनाव संकेंद्रण के प्रति अत्यधिक संवेदनशील होते हैं, जिससे चिपिंग और क्रैकिंग जैसी विफलताएँ होती हैं। निम्न-k पदार्थों की कम कठोरता और भंगुरता उन्हें यांत्रिक बल या तापीय तनाव के तहत, विशेष रूप से काटने के दौरान, संरचनात्मक क्षति के प्रति अधिक संवेदनशील बनाती है। उपकरण और वेफर सतह के बीच संपर्क, उच्च तापमान के साथ, तनाव संकेंद्रण को और बढ़ा सकता है।
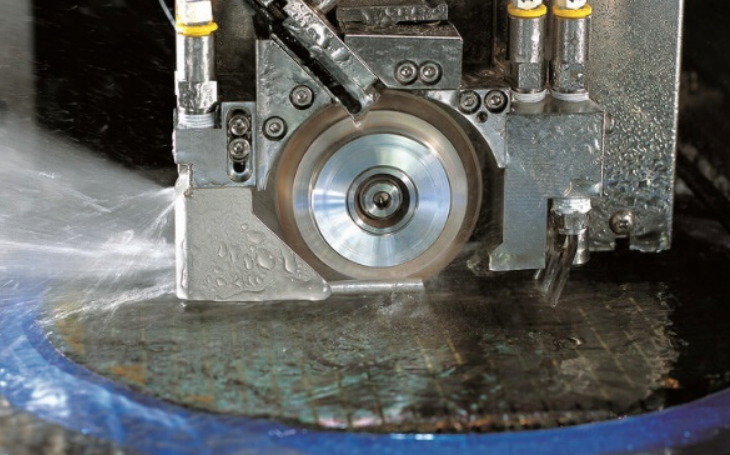
पदार्थ विज्ञान में प्रगति के साथ, वेफर डाइसिंग तकनीक पारंपरिक सिलिकॉन-आधारित अर्धचालकों से आगे बढ़कर गैलियम नाइट्राइड (GaN) जैसी नई सामग्रियों को भी शामिल करने लगी है। अपनी कठोरता और संरचनात्मक गुणों के कारण, ये नई सामग्रियाँ डाइसिंग प्रक्रियाओं के लिए नई चुनौतियाँ पेश करती हैं, जिसके लिए काटने के औज़ारों और तकनीकों में और सुधार की आवश्यकता है।
अर्धचालक उद्योग में एक महत्वपूर्ण प्रक्रिया के रूप में, वेफर डाइसिंग को विकसित होती मांगों और तकनीकी प्रगति के जवाब में अनुकूलित किया जा रहा है, जो भविष्य के माइक्रोइलेक्ट्रॉनिक्स और एकीकृत सर्किट प्रौद्योगिकियों के लिए आधार तैयार कर रहा है।
वेफर डाइसिंग तकनीक में सुधार सहायक सामग्रियों और उपकरणों के विकास से कहीं आगे तक जाते हैं। इनमें प्रक्रिया अनुकूलन, उपकरणों के प्रदर्शन में सुधार और डाइसिंग मापदंडों का सटीक नियंत्रण भी शामिल है। इन प्रगतियों का उद्देश्य वेफर डाइसिंग प्रक्रिया में उच्च परिशुद्धता, दक्षता और स्थिरता सुनिश्चित करना है, जिससे सेमीकंडक्टर उद्योग की छोटे आयामों, उच्च एकीकरण और अधिक जटिल चिप संरचनाओं की आवश्यकता पूरी हो सके।
सुधार क्षेत्र | विशिष्ट उपाय | प्रभाव |
प्रक्रिया अनुकूलन | - प्रारंभिक तैयारियों में सुधार, जैसे अधिक सटीक वेफर पोजिशनिंग और पथ नियोजन। | - काटने की त्रुटियों को कम करें और स्थिरता में सुधार करें। |
- काटने की त्रुटियों को न्यूनतम करें और स्थिरता को बढ़ाएं। | - उपकरण के दबाव, गति और तापमान को समायोजित करने के लिए वास्तविक समय की निगरानी और प्रतिक्रिया तंत्र को अपनाएं। | |
- वेफर टूटने की दर कम करें और चिप की गुणवत्ता में सुधार करें। | ||
उपकरण प्रदर्शन संवर्धन | - उच्च परिशुद्धता यांत्रिक प्रणालियों और उन्नत स्वचालन नियंत्रण प्रौद्योगिकी का उपयोग करें। | - काटने की सटीकता में वृद्धि और सामग्री की बर्बादी को कम करना। |
- उच्च कठोरता सामग्री वेफर्स के लिए उपयुक्त लेजर कटिंग प्रौद्योगिकी का परिचय। | - उत्पादन दक्षता में सुधार और मैन्युअल त्रुटियों में कमी। | |
- स्वचालित निगरानी और समायोजन के लिए उपकरण स्वचालन में वृद्धि। | ||
सटीक पैरामीटर नियंत्रण | - काटने की गहराई, गति, उपकरण प्रकार और शीतलन विधियों जैसे मापदंडों को बारीकी से समायोजित करें। | - डाई की अखंडता और विद्युत प्रदर्शन सुनिश्चित करें। |
- वेफर सामग्री, मोटाई और संरचना के आधार पर मापदंडों को अनुकूलित करें। | - उपज दर में वृद्धि, सामग्री की बर्बादी में कमी, तथा उत्पादन लागत में कमी। | |
सामरिक महत्व | - बाजार की मांग को पूरा करने के लिए लगातार नए तकनीकी रास्ते तलाशना, प्रक्रियाओं को अनुकूलित करना और उपकरण क्षमताओं को बढ़ाना। | - चिप निर्माण उपज और प्रदर्शन में सुधार, नई सामग्री और उन्नत चिप डिजाइन के विकास का समर्थन। |
1.2 वेफर डाइसिंग का महत्व
सेमीकंडक्टर निर्माण प्रक्रिया में वेफर डाइसिंग एक महत्वपूर्ण भूमिका निभाती है, जो बाद के चरणों के साथ-साथ अंतिम उत्पाद की गुणवत्ता और प्रदर्शन को भी सीधे प्रभावित करती है। इसके महत्व को इस प्रकार विस्तार से बताया जा सकता है:
सबसे पहले, चिप की उपज और विश्वसनीयता सुनिश्चित करने के लिए डाइसिंग की सटीकता और एकरूपता महत्वपूर्ण है। निर्माण के दौरान, वेफर्स कई जटिल सर्किट संरचनाओं को बनाने के लिए कई प्रसंस्करण चरणों से गुजरते हैं, जिन्हें अलग-अलग चिप्स (डाई) में सटीक रूप से विभाजित किया जाना चाहिए। यदि डाइसिंग प्रक्रिया के दौरान संरेखण या कटिंग में महत्वपूर्ण त्रुटियाँ होती हैं, तो सर्किट क्षतिग्रस्त हो सकते हैं, जिससे चिप की कार्यक्षमता और विश्वसनीयता प्रभावित हो सकती है। इसलिए, उच्च-परिशुद्धता वाली डाइसिंग तकनीक न केवल प्रत्येक चिप की अखंडता सुनिश्चित करती है, बल्कि आंतरिक सर्किट को होने वाली क्षति को भी रोकती है, जिससे समग्र उपज दर में सुधार होता है।
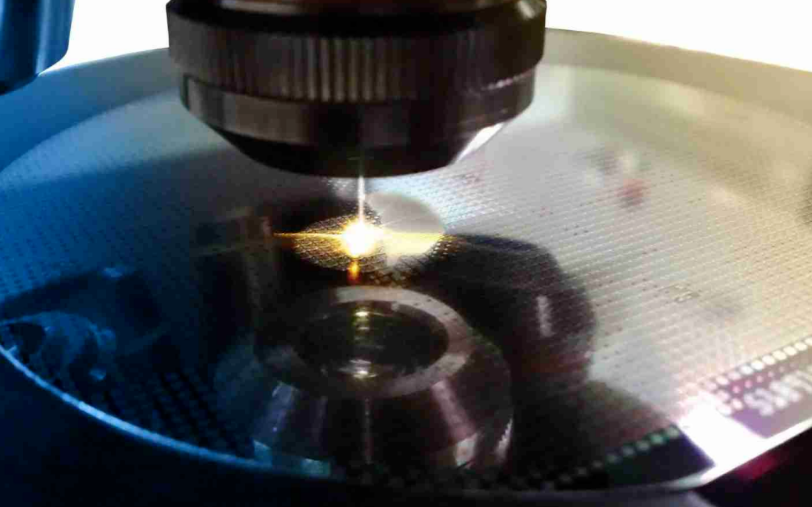
दूसरे, वेफर डाइसिंग का उत्पादन क्षमता और लागत नियंत्रण पर महत्वपूर्ण प्रभाव पड़ता है। निर्माण प्रक्रिया में एक महत्वपूर्ण चरण होने के नाते, इसकी दक्षता अगले चरणों की प्रगति को सीधे प्रभावित करती है। डाइसिंग प्रक्रिया को अनुकूलित करके, स्वचालन के स्तर को बढ़ाकर और काटने की गति में सुधार करके, समग्र उत्पादन क्षमता में उल्लेखनीय वृद्धि की जा सकती है।
दूसरी ओर, डाइसिंग के दौरान सामग्री की बर्बादी लागत प्रबंधन में एक महत्वपूर्ण कारक है। उन्नत डाइसिंग तकनीकों का उपयोग न केवल काटने की प्रक्रिया के दौरान अनावश्यक सामग्री की हानि को कम करता है, बल्कि वेफर उपयोग को भी बढ़ाता है, जिससे उत्पादन लागत कम होती है।
अर्धचालक प्रौद्योगिकी में प्रगति के साथ, वेफर का व्यास बढ़ता जा रहा है और परिपथ घनत्व भी उसी के अनुसार बढ़ रहा है, जिससे डाइसिंग प्रौद्योगिकी की माँग बढ़ रही है। बड़े वेफरों के लिए, विशेष रूप से उच्च-घनत्व वाले परिपथ क्षेत्रों में, कटिंग पथों पर अधिक सटीक नियंत्रण की आवश्यकता होती है, जहाँ मामूली विचलन भी कई चिप्स को ख़राब कर सकता है। इसके अतिरिक्त, बड़े वेफरों में अधिक कटिंग लाइनें और अधिक जटिल प्रक्रिया चरण शामिल होते हैं, जिससे इन चुनौतियों का सामना करने के लिए डाइसिंग प्रौद्योगिकियों की सटीकता, स्थिरता और दक्षता में और सुधार की आवश्यकता होती है।
1.3 वेफर डाइसिंग प्रक्रिया
वेफर डाइसिंग प्रक्रिया में तैयारी चरण से लेकर अंतिम गुणवत्ता निरीक्षण तक सभी चरण शामिल होते हैं, और प्रत्येक चरण कटे हुए चिप्स की गुणवत्ता और प्रदर्शन सुनिश्चित करने के लिए महत्वपूर्ण होता है। नीचे प्रत्येक चरण का विस्तृत विवरण दिया गया है।
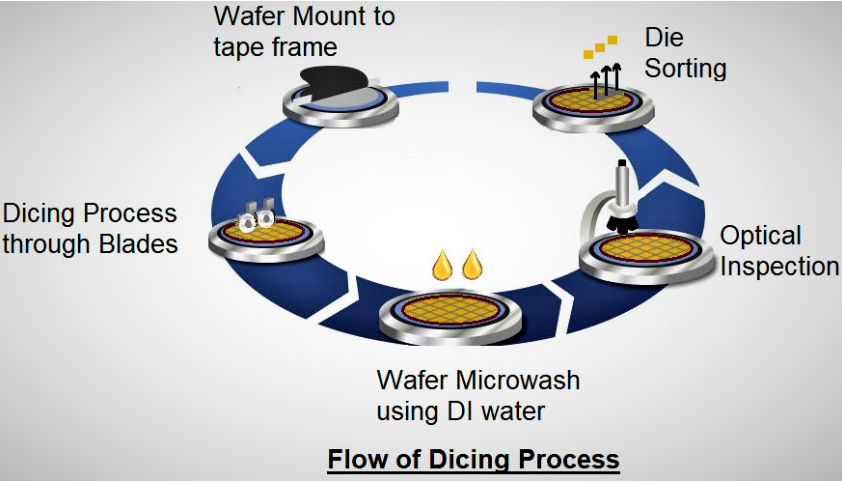
चरण | विस्तृत विवरण |
तैयारी चरण | -वेफर सफाई: अशुद्धियों, कणों और संदूषकों को हटाने के लिए अल्ट्रासोनिक या यांत्रिक स्क्रबिंग के साथ उच्च शुद्धता वाले पानी और विशेष सफाई एजेंटों का उपयोग करें, जिससे सतह साफ रहे। -सटीक स्थिति निर्धारण: यह सुनिश्चित करने के लिए उच्च परिशुद्धता वाले उपकरणों का उपयोग करें कि वेफर को डिज़ाइन किए गए कटिंग पथों के साथ सटीक रूप से विभाजित किया गया है। -वेफर फिक्सेशनकाटने के दौरान स्थिरता बनाए रखने के लिए वेफर को टेप फ्रेम पर सुरक्षित करें, ताकि कंपन या गति से होने वाली क्षति को रोका जा सके। |
काटने का चरण | -ब्लेड डाइसिंगभौतिक कटाई के लिए उच्च गति वाले घूर्णनशील हीरा-लेपित ब्लेड का उपयोग करें, जो सिलिकॉन-आधारित सामग्रियों के लिए उपयुक्त और लागत प्रभावी है। -लेजर डाइसिंग: गैर-संपर्क काटने के लिए उच्च ऊर्जा लेजर बीम का उपयोग करें, गैलियम नाइट्राइड जैसी भंगुर या उच्च कठोरता वाली सामग्रियों के लिए आदर्श, उच्च परिशुद्धता और कम सामग्री हानि प्रदान करता है। -नई तकनीकें: ताप-प्रभावित क्षेत्रों को न्यूनतम करते हुए दक्षता और परिशुद्धता में और अधिक सुधार करने के लिए लेजर और प्लाज्मा कटिंग प्रौद्योगिकियों का परिचय देना। |
सफाई चरण | - काटने के दौरान उत्पन्न मलबे और धूल को हटाने के लिए अल्ट्रासोनिक या स्प्रे सफाई के साथ विआयनीकृत जल (डीआई जल) और विशेष सफाई एजेंटों का उपयोग करें, जिससे अवशेषों को बाद की प्रक्रियाओं या चिप के विद्युत प्रदर्शन को प्रभावित करने से रोका जा सके। - उच्च शुद्धता वाला डीआई जल नए संदूषकों को आने से रोकता है, जिससे स्वच्छ वेफर वातावरण सुनिश्चित होता है। |
निरीक्षण चरण | -ऑप्टिकल निरीक्षण: दोषों की शीघ्र पहचान करने के लिए एआई एल्गोरिदम के साथ संयुक्त ऑप्टिकल डिटेक्शन सिस्टम का उपयोग करें, यह सुनिश्चित करें कि कटे हुए चिप्स में कोई दरार या टूटन न हो, निरीक्षण दक्षता में सुधार हो, और मानवीय त्रुटि कम हो। -आयाम मापसत्यापित करें कि चिप के आयाम डिज़ाइन विनिर्देशों के अनुरूप हैं। -विद्युत प्रदर्शन परीक्षण: सुनिश्चित करें कि महत्वपूर्ण चिप्स का विद्युत प्रदर्शन मानकों के अनुरूप हो, जिससे आगामी अनुप्रयोगों में विश्वसनीयता की गारंटी मिले। |
छंटाई चरण | - टेप फ्रेम से योग्य चिप्स को अलग करने के लिए रोबोटिक आर्म्स या वैक्यूम सक्शन कप का उपयोग करें और प्रदर्शन के आधार पर उन्हें स्वचालित रूप से छांटें, जिससे परिशुद्धता में सुधार करते हुए उत्पादन दक्षता और लचीलापन सुनिश्चित हो। |
वेफर कटिंग प्रक्रिया में वेफर की सफाई, स्थिति निर्धारण, कटिंग, सफाई, निरीक्षण और छंटाई शामिल है, और प्रत्येक चरण महत्वपूर्ण है। स्वचालन, लेज़र कटिंग और एआई निरीक्षण तकनीकों में प्रगति के साथ, आधुनिक वेफर कटिंग प्रणालियाँ उच्च परिशुद्धता, गति और कम सामग्री हानि प्राप्त कर सकती हैं। भविष्य में, लेज़र और प्लाज़्मा जैसी नई कटिंग तकनीकें धीरे-धीरे पारंपरिक ब्लेड कटिंग की जगह ले लेंगी ताकि बढ़ती जटिल चिप डिज़ाइनों की ज़रूरतों को पूरा किया जा सके, जिससे सेमीकंडक्टर निर्माण प्रक्रियाओं के विकास को और गति मिलेगी।
वेफर कटिंग तकनीक और इसके सिद्धांत
चित्र में तीन सामान्य वेफर कटिंग प्रौद्योगिकियों को दर्शाया गया है:ब्लेड डाइसिंग,लेजर डाइसिंग, औरप्लाज्मा डाइसिंगनीचे इन तीन तकनीकों का विस्तृत विश्लेषण और पूरक व्याख्या दी गई है:
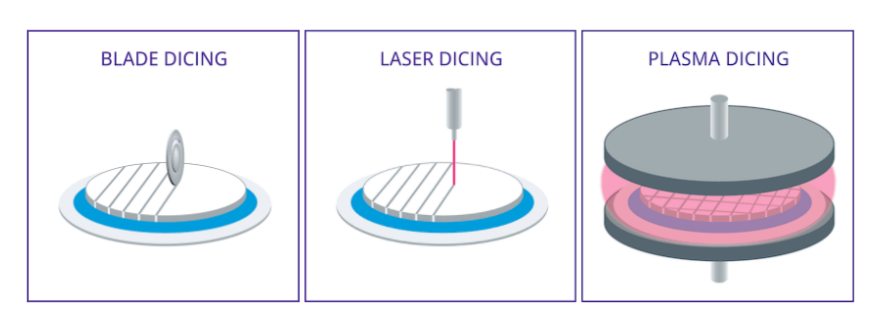
अर्धचालक निर्माण में, वेफर कटिंग एक महत्वपूर्ण चरण है जिसके लिए वेफर की मोटाई के आधार पर उपयुक्त कटिंग विधि का चयन करना आवश्यक है। पहला चरण वेफर की मोटाई निर्धारित करना है। यदि वेफर की मोटाई 100 माइक्रोन से अधिक है, तो ब्लेड डाइसिंग को कटिंग विधि के रूप में चुना जा सकता है। यदि ब्लेड डाइसिंग उपयुक्त नहीं है, तो फ्रैक्चर डाइसिंग विधि का उपयोग किया जा सकता है, जिसमें स्क्राइब कटिंग और ब्लेड डाइसिंग दोनों तकनीकें शामिल हैं।
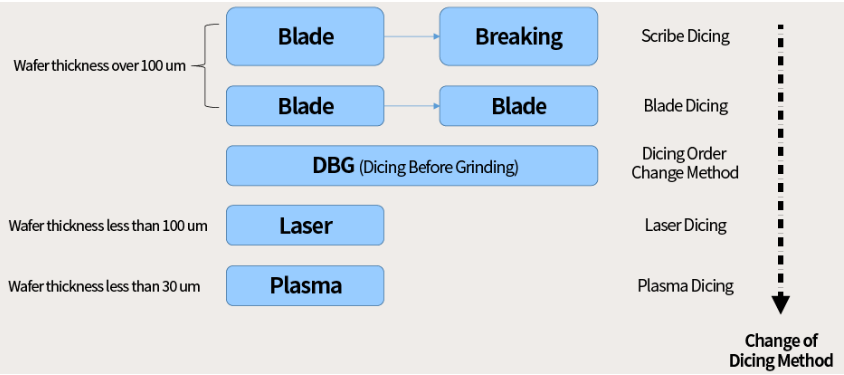
जब वेफर की मोटाई 30 से 100 माइक्रोन के बीच हो, तो DBG (पीसने से पहले डाइस) विधि की सलाह दी जाती है। इस स्थिति में, सर्वोत्तम परिणाम प्राप्त करने के लिए स्क्राइब कटिंग, ब्लेड डाइसिंग, या आवश्यकतानुसार कटिंग क्रम को समायोजित करने का विकल्प चुना जा सकता है।
30 माइक्रोन से कम मोटाई वाले अति-पतले वेफ़र्स के लिए, लेज़र कटिंग पसंदीदा तरीका बन जाता है क्योंकि यह पतले वेफ़र्स को बिना ज़्यादा नुकसान पहुँचाए सटीक रूप से काटने में सक्षम होता है। यदि लेज़र कटिंग विशिष्ट आवश्यकताओं को पूरा नहीं कर पाती है, तो प्लाज़्मा कटिंग को एक विकल्प के रूप में इस्तेमाल किया जा सकता है। यह फ़्लोचार्ट विभिन्न मोटाई की स्थितियों के लिए सबसे उपयुक्त वेफ़र कटिंग तकनीक का चयन सुनिश्चित करने के लिए एक स्पष्ट निर्णय लेने का मार्ग प्रदान करता है।
2.1 यांत्रिक कटिंग तकनीक
यांत्रिक कटिंग तकनीक वेफर डाइसिंग की पारंपरिक विधि है। इसका मूल सिद्धांत वेफर को काटने के लिए एक उच्च गति वाले घूर्णनशील हीरा ग्राइंडिंग व्हील का उपयोग कटिंग टूल के रूप में करना है। मुख्य उपकरण में एक एयर-बेयरिंग स्पिंडल शामिल है, जो हीरा ग्राइंडिंग व्हील टूल को उच्च गति पर चलाकर एक पूर्वनिर्धारित कटिंग पथ पर सटीक कटिंग या ग्रूविंग करता है। इस तकनीक का उद्योग में व्यापक रूप से उपयोग इसकी कम लागत, उच्च दक्षता और व्यापक प्रयोज्यता के कारण किया जाता है।
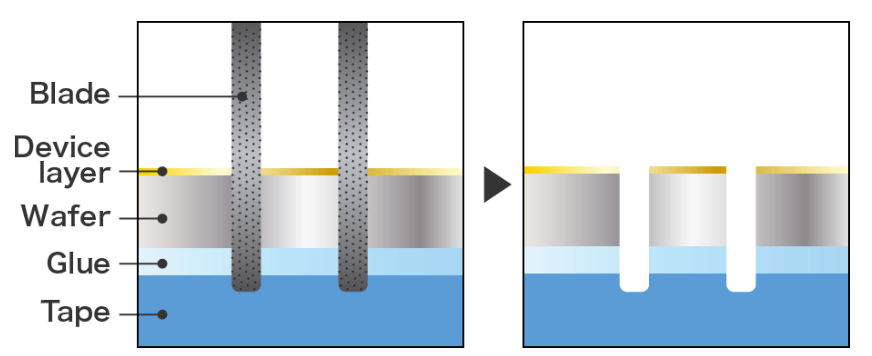
लाभ
हीरा पीसने वाले पहिये के औज़ारों की उच्च कठोरता और घिसाव प्रतिरोधकता, यांत्रिक कटाई तकनीक को विभिन्न वेफर सामग्रियों की कटाई आवश्यकताओं के अनुकूल बनाने में सक्षम बनाती है, चाहे वे पारंपरिक सिलिकॉन-आधारित सामग्री हों या नए यौगिक अर्धचालक। इसका संचालन सरल है और तकनीकी आवश्यकताएँ अपेक्षाकृत कम हैं, जिससे बड़े पैमाने पर उत्पादन में इसकी लोकप्रियता और भी बढ़ जाती है। इसके अतिरिक्त, लेज़र कटिंग जैसी अन्य कटाई विधियों की तुलना में, यांत्रिक कटाई की लागत अधिक नियंत्रणीय होती है, जिससे यह उच्च-मात्रा उत्पादन आवश्यकताओं के लिए उपयुक्त हो जाती है।
सीमाएँ
इसके अनेक लाभों के बावजूद, यांत्रिक कटिंग तकनीक की कुछ सीमाएँ भी हैं। पहला, उपकरण और वेफर के बीच भौतिक संपर्क के कारण, कटिंग की सटीकता अपेक्षाकृत सीमित होती है, जिससे अक्सर आयामी विचलन होता है जो बाद में चिप पैकेजिंग और परीक्षण की सटीकता को प्रभावित कर सकता है। दूसरा, यांत्रिक कटिंग प्रक्रिया के दौरान चिपिंग और दरारें जैसे दोष आसानी से उत्पन्न हो सकते हैं, जो न केवल उपज दर को प्रभावित करते हैं, बल्कि चिप्स की विश्वसनीयता और जीवनकाल पर भी नकारात्मक प्रभाव डाल सकते हैं। यांत्रिक तनाव-जनित क्षति उच्च-घनत्व वाले चिप निर्माण के लिए विशेष रूप से हानिकारक है, खासकर भंगुर पदार्थों को काटते समय, जहाँ ये समस्याएँ अधिक प्रमुख होती हैं।
तकनीकी सुधार
इन सीमाओं को दूर करने के लिए, शोधकर्ता यांत्रिक काटने की प्रक्रिया को लगातार अनुकूलित कर रहे हैं। प्रमुख सुधारों में काटने की सटीकता और स्थायित्व में सुधार के लिए ग्राइंडिंग व्हील्स के डिज़ाइन और सामग्री चयन में सुधार शामिल है। इसके अतिरिक्त, काटने वाले उपकरणों के संरचनात्मक डिज़ाइन और नियंत्रण प्रणालियों के अनुकूलन ने काटने की प्रक्रिया की स्थिरता और स्वचालन में और सुधार किया है। ये प्रगति मानवीय संचालन से होने वाली त्रुटियों को कम करती है और कट्स की एकरूपता में सुधार करती है। काटने की प्रक्रिया के दौरान विसंगतियों की वास्तविक समय निगरानी के लिए उन्नत निरीक्षण और गुणवत्ता नियंत्रण तकनीकों की शुरूआत ने भी काटने की विश्वसनीयता और उत्पादकता में उल्लेखनीय सुधार किया है।
भविष्य का विकास और नई प्रौद्योगिकियाँ
यद्यपि यांत्रिक कटिंग तकनीक अभी भी वेफर कटिंग में एक महत्वपूर्ण स्थान रखती है, अर्धचालक प्रक्रियाओं के विकास के साथ-साथ नई कटिंग तकनीकें तेज़ी से आगे बढ़ रही हैं। उदाहरण के लिए, थर्मल लेज़र कटिंग तकनीक का अनुप्रयोग यांत्रिक कटिंग में सटीकता और दोष संबंधी समस्याओं के नए समाधान प्रदान करता है। यह गैर-संपर्क कटिंग विधि वेफर पर भौतिक तनाव को कम करती है, जिससे चिपिंग और क्रैकिंग की संभावना काफी कम हो जाती है, खासकर अधिक भंगुर पदार्थों को काटते समय। भविष्य में, उभरती हुई कटिंग तकनीकों के साथ यांत्रिक कटिंग तकनीक का एकीकरण अर्धचालक निर्माण को अधिक विकल्प और लचीलापन प्रदान करेगा, जिससे विनिर्माण दक्षता और चिप गुणवत्ता में और वृद्धि होगी।
निष्कर्षतः, यद्यपि यांत्रिक कटाई प्रौद्योगिकी में कुछ कमियां हैं, फिर भी निरंतर तकनीकी सुधार और नई कटाई तकनीकों के साथ इसका एकीकरण इसे अभी भी अर्धचालक विनिर्माण में महत्वपूर्ण भूमिका निभाने और भविष्य की प्रक्रियाओं में अपनी प्रतिस्पर्धात्मकता बनाए रखने की अनुमति देता है।
2.2 लेज़र कटिंग तकनीक
वेफर कटिंग की एक नई विधि के रूप में, लेज़र कटिंग तकनीक ने अपनी उच्च परिशुद्धता, यांत्रिक संपर्क क्षति की कमी और तीव्र कटिंग क्षमताओं के कारण अर्धचालक उद्योग में धीरे-धीरे व्यापक ध्यान आकर्षित किया है। यह तकनीक वेफर सामग्री की सतह पर एक छोटा सा ऊष्मा-प्रभावित क्षेत्र बनाने के लिए लेज़र बीम की उच्च ऊर्जा घनत्व और फोकसिंग क्षमता का उपयोग करती है। जब लेज़र बीम को वेफर पर लगाया जाता है, तो उत्पन्न तापीय तनाव सामग्री को निर्दिष्ट स्थान पर फ्रैक्चर कर देता है, जिससे सटीक कटिंग प्राप्त होती है।
लेजर कटिंग प्रौद्योगिकी के लाभ
• उच्चा परिशुद्धिलेजर बीम की सटीक स्थिति निर्धारण क्षमता माइक्रोन या नैनोमीटर स्तर की परिशुद्धता के साथ काटने की अनुमति देती है, जो आधुनिक उच्च परिशुद्धता, उच्च घनत्व वाले एकीकृत सर्किट विनिर्माण की आवश्यकताओं को पूरा करती है।
• कोई यांत्रिक संपर्क नहींलेजर कटिंग वेफर के साथ भौतिक संपर्क से बचाती है, जिससे यांत्रिक कटिंग में होने वाली सामान्य समस्याओं, जैसे कि छिलना और दरार पड़ना, को रोका जा सकता है, तथा चिप्स की उपज दर और विश्वसनीयता में महत्वपूर्ण सुधार होता है।
• तेज़ काटने की गतिलेजर कटिंग की उच्च गति उत्पादन दक्षता में वृद्धि में योगदान देती है, जिससे यह बड़े पैमाने पर, उच्च गति वाले उत्पादन परिदृश्यों के लिए विशेष रूप से उपयुक्त हो जाती है।
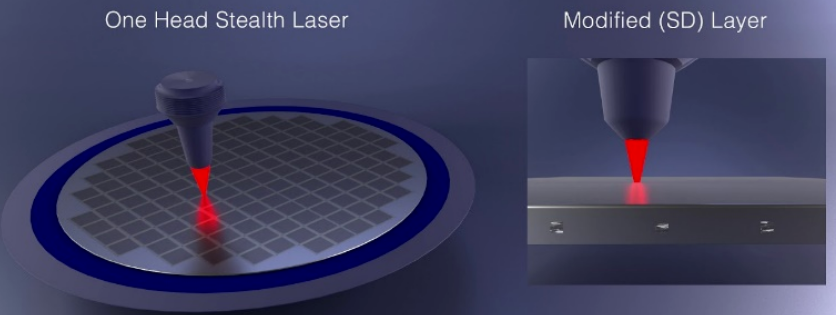
चुनौतियों का सामना
• उच्च उपकरण लागतलेजर कटिंग उपकरण के लिए प्रारंभिक निवेश अधिक है, जो आर्थिक दबाव प्रस्तुत करता है, विशेष रूप से छोटे से मध्यम आकार के उत्पादन उद्यमों के लिए।
• जटिल प्रक्रिया नियंत्रणलेजर कटिंग में ऊर्जा घनत्व, फोकस स्थिति और कटिंग गति सहित कई मापदंडों के सटीक नियंत्रण की आवश्यकता होती है, जिससे प्रक्रिया जटिल हो जाती है।
• ताप-प्रभावित क्षेत्र के मुद्देयद्यपि लेज़र कटिंग की गैर-संपर्क प्रकृति यांत्रिक क्षति को कम करती है, ऊष्मा-प्रभावित क्षेत्र (HAZ) के कारण उत्पन्न तापीय तनाव वेफर सामग्री के गुणों पर नकारात्मक प्रभाव डाल सकता है। इस प्रभाव को कम करने के लिए प्रक्रिया के और अधिक अनुकूलन की आवश्यकता है।
तकनीकी सुधार के निर्देश
इन चुनौतियों से निपटने के लिए, शोधकर्ता उपकरण लागत को कम करने, कटाई दक्षता में सुधार लाने और प्रक्रिया प्रवाह को अनुकूलित करने पर ध्यान केंद्रित कर रहे हैं।
• कुशल लेज़र और ऑप्टिकल सिस्टमअधिक कुशल लेजर और उन्नत ऑप्टिकल प्रणालियों को विकसित करके, काटने की सटीकता और गति को बढ़ाते हुए उपकरणों की लागत को कम करना संभव है।
• प्रक्रिया मापदंडों का अनुकूलनलेजर और वेफर सामग्रियों के बीच परस्पर क्रिया पर गहन शोध किया जा रहा है, ताकि ऐसी प्रक्रियाओं में सुधार किया जा सके जो ताप-प्रभावित क्षेत्र को कम कर सकें, जिससे काटने की गुणवत्ता में सुधार हो सके।
• बुद्धिमान नियंत्रण प्रणालीबुद्धिमान नियंत्रण प्रौद्योगिकियों के विकास का उद्देश्य लेजर कटिंग प्रक्रिया को स्वचालित और अनुकूलित करना है, जिससे इसकी स्थिरता और स्थिरता में सुधार हो सके।
लेज़र कटिंग तकनीक अति-पतले वेफ़र्स और उच्च-परिशुद्धता कटिंग परिदृश्यों में विशेष रूप से प्रभावी है। जैसे-जैसे वेफ़र्स का आकार बढ़ता है और सर्किट घनत्व बढ़ता है, पारंपरिक यांत्रिक कटिंग विधियाँ आधुनिक अर्धचालक निर्माण की उच्च-परिशुद्धता और उच्च-दक्षता की माँगों को पूरा करने में संघर्ष करती हैं। अपने अनूठे लाभों के कारण, लेज़र कटिंग इन क्षेत्रों में पसंदीदा समाधान बनता जा रहा है।
हालाँकि लेज़र कटिंग तकनीक अभी भी उच्च उपकरण लागत और प्रक्रिया जटिलता जैसी चुनौतियों का सामना कर रही है, उच्च परिशुद्धता और गैर-संपर्क क्षति में इसके अनूठे लाभ इसे सेमीकंडक्टर निर्माण में विकास की एक महत्वपूर्ण दिशा बनाते हैं। जैसे-जैसे लेज़र तकनीक और बुद्धिमान नियंत्रण प्रणालियाँ आगे बढ़ रही हैं, लेज़र कटिंग से वेफर कटिंग की दक्षता और गुणवत्ता में और सुधार होने की उम्मीद है, जिससे सेमीकंडक्टर उद्योग का निरंतर विकास होगा।
2.3 प्लाज्मा कटिंग तकनीक
हाल के वर्षों में, एक उभरती हुई वेफर डाइसिंग विधि के रूप में, प्लाज्मा कटिंग तकनीक ने काफ़ी ध्यान आकर्षित किया है। यह तकनीक उच्च-ऊर्जा प्लाज्मा बीम का उपयोग करके, प्लाज्मा बीम की ऊर्जा, गति और कटिंग पथ को नियंत्रित करके, वेफर्स को सटीक रूप से काटती है, जिससे सर्वोत्तम कटिंग परिणाम प्राप्त होते हैं।
कार्य सिद्धांत और लाभ
प्लाज़्मा कटिंग की प्रक्रिया उपकरण द्वारा उत्पन्न उच्च-तापमान, उच्च-ऊर्जा प्लाज़्मा बीम पर निर्भर करती है। यह बीम वेफर सामग्री को बहुत कम समय में उसके गलनांक या वाष्पीकरण बिंदु तक गर्म कर सकती है, जिससे तेज़ कटिंग संभव हो पाती है। पारंपरिक यांत्रिक या लेज़र कटिंग की तुलना में, प्लाज़्मा कटिंग तेज़ होती है और एक छोटा ऊष्मा-प्रभावित क्षेत्र बनाती है, जिससे कटिंग के दौरान दरारें और क्षति की संभावना प्रभावी रूप से कम हो जाती है।
व्यावहारिक अनुप्रयोगों में, प्लाज़्मा कटिंग तकनीक जटिल आकृतियों वाले वेफ़र्स को संभालने में विशेष रूप से कुशल है। इसकी उच्च-ऊर्जा, समायोज्य प्लाज़्मा बीम अनियमित आकार के वेफ़र्स को उच्च परिशुद्धता के साथ आसानी से काट सकती है। इसलिए, माइक्रोइलेक्ट्रॉनिक्स निर्माण में, विशेष रूप से उच्च-स्तरीय चिप्स के अनुकूलित और छोटे बैच उत्पादन में, यह तकनीक व्यापक उपयोग के लिए अपार संभावनाएं दिखाती है।
चुनौतियाँ और सीमाएँ
प्लाज्मा कटिंग तकनीक के अनेक लाभों के बावजूद, इसमें कुछ चुनौतियां भी हैं।
• जटिल प्रक्रियाप्लाज्मा कटिंग प्रक्रिया जटिल है और इसे सुनिश्चित करने के लिए उच्च परिशुद्धता वाले उपकरण और अनुभवी ऑपरेटरों की आवश्यकता होती हैकाटने में सटीकता और स्थिरता।
• पर्यावरण नियंत्रण और सुरक्षाप्लाज्मा बीम की उच्च तापमान, उच्च ऊर्जा प्रकृति के कारण कड़े पर्यावरण नियंत्रण और सुरक्षा उपायों की आवश्यकता होती है, जिससे कार्यान्वयन की जटिलता और लागत बढ़ जाती है।
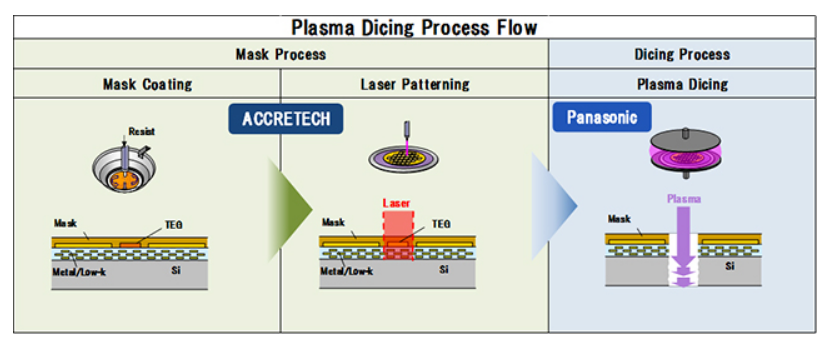
भविष्य के विकास की दिशाएँ
तकनीकी प्रगति के साथ, प्लाज़्मा कटिंग से जुड़ी चुनौतियों का धीरे-धीरे समाधान होने की उम्मीद है। अधिक कुशल और स्थिर कटिंग उपकरण विकसित करके, मैन्युअल संचालन पर निर्भरता कम की जा सकती है, जिससे उत्पादन क्षमता में सुधार होगा। साथ ही, प्रक्रिया मापदंडों और कटिंग वातावरण को अनुकूलित करने से सुरक्षा जोखिमों और परिचालन लागतों को कम करने में मदद मिलेगी।
सेमीकंडक्टर उद्योग में, वेफर कटिंग और डाइसिंग तकनीक में नवाचार उद्योग के विकास को गति देने के लिए महत्वपूर्ण हैं। अपनी उच्च परिशुद्धता, दक्षता और जटिल वेफर आकृतियों को संभालने की क्षमता के साथ, प्लाज्मा कटिंग तकनीक इस क्षेत्र में एक महत्वपूर्ण नई खिलाड़ी के रूप में उभरी है। हालाँकि कुछ चुनौतियाँ अभी भी बनी हुई हैं, लेकिन निरंतर तकनीकी नवाचार के साथ इन मुद्दों का धीरे-धीरे समाधान किया जाएगा, जिससे सेमीकंडक्टर निर्माण में और अधिक संभावनाएँ और अवसर पैदा होंगे।
प्लाज़्मा कटिंग तकनीक की अनुप्रयोग संभावनाएँ व्यापक हैं और भविष्य में सेमीकंडक्टर निर्माण में इसकी और भी महत्वपूर्ण भूमिका होने की उम्मीद है। निरंतर तकनीकी नवाचार और अनुकूलन के माध्यम से, प्लाज़्मा कटिंग न केवल मौजूदा चुनौतियों का समाधान करेगी, बल्कि सेमीकंडक्टर उद्योग के विकास का एक शक्तिशाली चालक भी बनेगी।
2.4 कटिंग की गुणवत्ता और प्रभावित करने वाले कारक
वेफर कटिंग की गुणवत्ता, बाद में चिप पैकेजिंग, परीक्षण और अंतिम उत्पाद के समग्र प्रदर्शन और विश्वसनीयता के लिए महत्वपूर्ण है। कटिंग के दौरान आने वाली आम समस्याओं में दरारें, छिलना और कटिंग विचलन शामिल हैं। ये समस्याएँ कई कारकों के एक साथ काम करने से प्रभावित होती हैं।
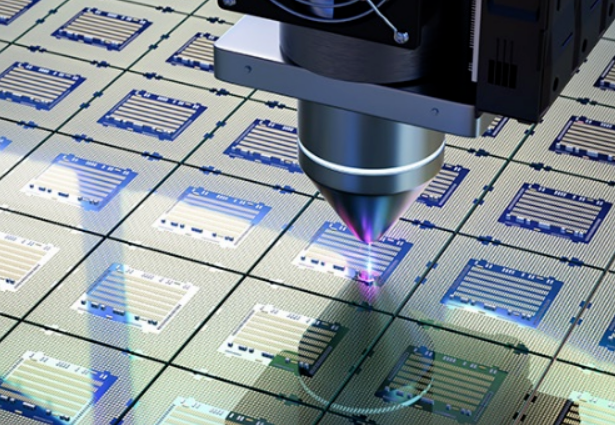
वर्ग | सामग्री | प्रभाव |
प्रक्रिया पैरामीटर | काटने की गति, फ़ीड दर और काटने की गहराई, काटने की प्रक्रिया की स्थिरता और सटीकता को सीधे प्रभावित करती हैं। अनुचित सेटिंग्स तनाव संकेंद्रण और अत्यधिक ताप-प्रभावित क्षेत्र का कारण बन सकती हैं, जिसके परिणामस्वरूप दरारें और छिलने की समस्या हो सकती है। वेफर सामग्री, मोटाई और काटने की आवश्यकताओं के आधार पर मापदंडों को उचित रूप से समायोजित करना वांछित काटने के परिणाम प्राप्त करने की कुंजी है। | सही प्रक्रिया पैरामीटर सटीक कटाई सुनिश्चित करते हैं और दरारें और छिलने जैसे दोषों के जोखिम को कम करते हैं। |
उपकरण और सामग्री कारक | -ब्लेड की गुणवत्ताब्लेड की सामग्री, कठोरता और घिसाव प्रतिरोध, काटने की प्रक्रिया की चिकनाई और कटी हुई सतह की समतलता को प्रभावित करते हैं। खराब गुणवत्ता वाले ब्लेड घर्षण और तापीय तनाव को बढ़ाते हैं, जिससे दरारें या छिलने की संभावना बढ़ जाती है। ब्लेड की सही सामग्री का चयन करना महत्वपूर्ण है। -शीतलक प्रदर्शनशीतलक काटने के तापमान को कम करने, घर्षण को कम करने और मलबे को साफ करने में मदद करते हैं। अप्रभावी शीतलक उच्च तापमान और मलबे के जमाव का कारण बन सकता है, जिससे काटने की गुणवत्ता और दक्षता प्रभावित होती है। कुशल और पर्यावरण के अनुकूल शीतलक का चयन करना महत्वपूर्ण है। | ब्लेड की गुणवत्ता कट की सटीकता और चिकनाई को प्रभावित करती है। अप्रभावी शीतलक के कारण कटिंग की गुणवत्ता और दक्षता खराब हो सकती है, जिससे शीतलक के इष्टतम उपयोग की आवश्यकता पर ज़ोर पड़ता है। |
प्रक्रिया नियंत्रण और गुणवत्ता निरीक्षण | -प्रक्रिया नियंत्रणकाटने की प्रक्रिया में स्थिरता और एकरूपता सुनिश्चित करने के लिए प्रमुख काटने के मापदंडों की वास्तविक समय निगरानी और समायोजन। -गुणवत्ता निरीक्षणकाटने के बाद उपस्थिति की जांच, आयामी माप और विद्युत प्रदर्शन परीक्षण गुणवत्ता संबंधी मुद्दों को तुरंत पहचानने और उनका समाधान करने में मदद करते हैं, जिससे काटने की सटीकता और स्थिरता में सुधार होता है। | उचित प्रक्रिया नियंत्रण और गुणवत्ता निरीक्षण, लगातार, उच्च गुणवत्ता वाले कटिंग परिणाम सुनिश्चित करने और संभावित समस्याओं का शीघ्र पता लगाने में मदद करते हैं। |

काटने की गुणवत्ता में सुधार
कटिंग की गुणवत्ता में सुधार के लिए एक व्यापक दृष्टिकोण की आवश्यकता होती है जिसमें प्रक्रिया मापदंडों, उपकरणों और सामग्री के चयन, प्रक्रिया नियंत्रण और निरीक्षण को ध्यान में रखा जाता है। कटिंग तकनीकों को लगातार परिष्कृत करके और प्रक्रिया विधियों को अनुकूलित करके, वेफर कटिंग की सटीकता और स्थिरता को और बढ़ाया जा सकता है, जिससे सेमीकंडक्टर निर्माण उद्योग को अधिक विश्वसनीय तकनीकी सहायता मिल सकती है।
#03 काटने के बाद की हैंडलिंग और परीक्षण
3.1 सफाई और सुखाना
वेफर कटिंग के बाद सफाई और सुखाने के चरण चिप की गुणवत्ता और आगे की प्रक्रियाओं की सुचारू प्रगति सुनिश्चित करने के लिए महत्वपूर्ण हैं। इस चरण के दौरान, सिलिकॉन मलबे, शीतलक अवशेषों और कटिंग के दौरान उत्पन्न अन्य दूषित पदार्थों को पूरी तरह से हटाना आवश्यक है। यह सुनिश्चित करना भी उतना ही महत्वपूर्ण है कि सफाई प्रक्रिया के दौरान चिप्स क्षतिग्रस्त न हों, और सुखाने के बाद, सुनिश्चित करें कि चिप की सतह पर कोई नमी न रहे ताकि जंग या इलेक्ट्रोस्टैटिक डिस्चार्ज जैसी समस्याओं से बचा जा सके।
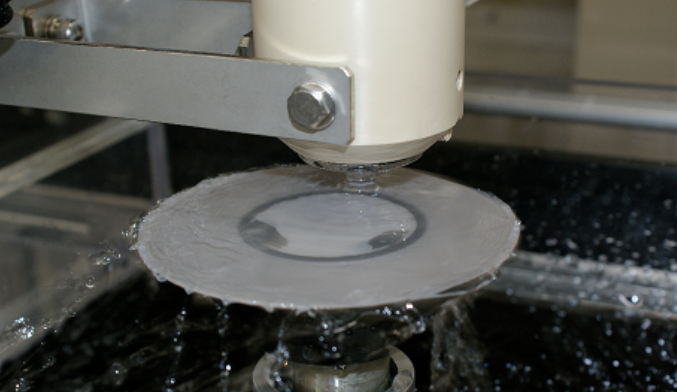
काटने के बाद की देखभाल: सफाई और सुखाने की प्रक्रिया
प्रक्रिया चरण | सामग्री | प्रभाव |
सफाई प्रक्रिया | -तरीकासफाई के लिए विशेष सफाई एजेंटों और शुद्ध पानी का उपयोग करें, साथ ही अल्ट्रासोनिक या मैकेनिकल ब्रशिंग तकनीक का भी उपयोग करें। | यह सुनिश्चित करता है कि संदूषक पूरी तरह से हटा दिए जाएं तथा सफाई के दौरान चिप्स को नुकसान से बचाया जाए। |
-सफाई एजेंट का चयनचिप को नुकसान पहुंचाए बिना प्रभावी सफाई सुनिश्चित करने के लिए वेफर सामग्री और संदूषक प्रकार के आधार पर चयन करें। | प्रभावी सफाई और चिप संरक्षण के लिए उचित एजेंट का चयन महत्वपूर्ण है। | |
-पैरामीटर नियंत्रणअनुचित सफाई के कारण होने वाली गुणवत्ता संबंधी समस्याओं को रोकने के लिए सफाई के तापमान, समय और सफाई समाधान की सांद्रता को सख्ती से नियंत्रित करें। | नियंत्रण वेफर को नुकसान पहुंचाने या दूषित पदार्थ छोड़ने से बचाने में मदद करते हैं, जिससे निरंतर गुणवत्ता सुनिश्चित होती है। | |
सुखाने की प्रक्रिया | -पारंपरिक तरीकेप्राकृतिक वायु सुखाने और गर्म वायु सुखाने, जिनकी दक्षता कम होती है और जिनसे स्थैतिक विद्युत का निर्माण हो सकता है। | इसके परिणामस्वरूप सुखाने का समय धीमा हो सकता है और संभावित स्थैतिक समस्याएं हो सकती हैं। |
-आधुनिक प्रौद्योगिकियां: यह सुनिश्चित करने के लिए कि चिप्स जल्दी सूख जाएं और हानिकारक प्रभावों से बचें, वैक्यूम सुखाने और इन्फ्रारेड सुखाने जैसी उन्नत तकनीकों का उपयोग करें। | सुखाने की प्रक्रिया अधिक तीव्र और कुशल होती है, जिससे स्थैतिक उत्सर्जन या नमी संबंधी समस्याओं का जोखिम कम हो जाता है। | |
उपकरण चयन और रखरखाव | -उपकरण चयनउच्च प्रदर्शन वाली सफाई और सुखाने वाली मशीनें प्रसंस्करण दक्षता में सुधार करती हैं और हैंडलिंग के दौरान संभावित समस्याओं को नियंत्रित करती हैं। | उच्च गुणवत्ता वाली मशीनें बेहतर प्रसंस्करण सुनिश्चित करती हैं और सफाई और सुखाने के दौरान त्रुटियों की संभावना को कम करती हैं। |
-उपकरण रखरखावउपकरणों का नियमित निरीक्षण और रखरखाव यह सुनिश्चित करता है कि वे सर्वोत्तम कार्यशील स्थिति में रहें, जिससे चिप की गुणवत्ता की गारंटी मिलती है। | उचित रखरखाव उपकरण की विफलताओं को रोकता है, तथा विश्वसनीय और उच्च गुणवत्ता वाली प्रसंस्करण सुनिश्चित करता है। |
काटने के बाद सफाई और सुखाना
वेफर कटिंग के बाद सफाई और सुखाने के चरण जटिल और नाजुक प्रक्रियाएं हैं, जिनमें अंतिम प्रसंस्करण परिणाम सुनिश्चित करने के लिए कई कारकों पर सावधानीपूर्वक विचार करने की आवश्यकता होती है। वैज्ञानिक तरीकों और कठोर प्रक्रियाओं का उपयोग करके, यह सुनिश्चित करना संभव है कि प्रत्येक चिप बाद की पैकेजिंग और परीक्षण चरणों में इष्टतम स्थिति में प्रवेश करे।
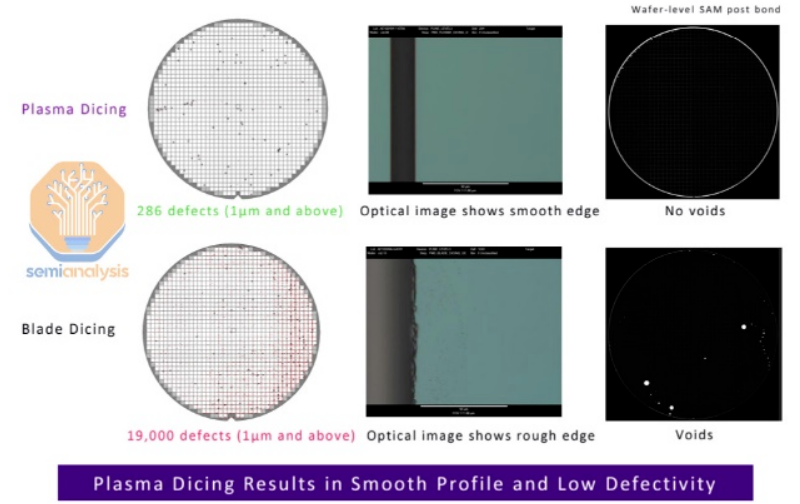
काटने के बाद निरीक्षण और परीक्षण
कदम | सामग्री | प्रभाव |
निरीक्षण चरण | 1.दृश्य निरीक्षण: चिप की सतह पर दरारें, छिलने या संदूषण जैसे दिखाई देने वाले दोषों की जांच करने के लिए दृश्य या स्वचालित निरीक्षण उपकरण का उपयोग करें। बर्बादी से बचने के लिए शारीरिक रूप से क्षतिग्रस्त चिप्स की तुरंत पहचान करें। | प्रक्रिया के प्रारंभ में ही दोषपूर्ण चिप्स की पहचान करने और उन्हें हटाने में मदद करता है, जिससे सामग्री की हानि कम होती है। |
2.आकार मापचिप के आयामों को सटीक रूप से मापने के लिए सटीक माप उपकरणों का उपयोग करें, यह सुनिश्चित करें कि कट का आकार डिजाइन विनिर्देशों के अनुरूप हो और प्रदर्शन संबंधी समस्याओं या पैकेजिंग कठिनाइयों को रोका जा सके। | यह सुनिश्चित करता है कि चिप्स आवश्यक आकार सीमा के भीतर हों, जिससे प्रदर्शन में गिरावट या संयोजन संबंधी समस्याओं को रोका जा सके। | |
3.विद्युत प्रदर्शन परीक्षणप्रतिरोध, धारिता और प्रेरकत्व जैसे प्रमुख विद्युतीय मापदंडों का मूल्यांकन करें, ताकि गैर-अनुपालक चिप्स की पहचान की जा सके और यह सुनिश्चित किया जा सके कि केवल प्रदर्शन-योग्य चिप्स ही अगले चरण में आगे बढ़ें। | यह सुनिश्चित करता है कि प्रक्रिया में केवल कार्यात्मक और प्रदर्शन-परीक्षित चिप्स ही आगे बढ़ें, जिससे बाद के चरणों में विफलता का जोखिम कम हो जाता है। | |
परीक्षण चरण | 1.क्रियात्मक परीक्षणसत्यापित करें कि चिप की मूल कार्यक्षमता अपेक्षित रूप से काम कर रही है, कार्यात्मक असामान्यताओं वाले चिप्स की पहचान करें और उन्हें हटा दें। | यह सुनिश्चित करता है कि चिप्स बाद के चरणों में आगे बढ़ने से पहले बुनियादी परिचालन आवश्यकताओं को पूरा करें। |
2.विश्वसनीयता परीक्षणलंबे समय तक उपयोग या कठोर वातावरण में चिप के प्रदर्शन की स्थिरता का मूल्यांकन करना, जिसमें आमतौर पर उच्च तापमान पर उम्र बढ़ना, कम तापमान पर परीक्षण और वास्तविक दुनिया की चरम स्थितियों का अनुकरण करने के लिए आर्द्रता परीक्षण शामिल होता है। | यह सुनिश्चित करता है कि चिप्स विभिन्न पर्यावरणीय परिस्थितियों में विश्वसनीय रूप से कार्य कर सकें, जिससे उत्पाद की दीर्घायु और स्थिरता में सुधार हो। | |
3.संगतता परीक्षणसत्यापित करें कि चिप अन्य घटकों या प्रणालियों के साथ ठीक से काम करती है, तथा यह सुनिश्चित करें कि असंगतता के कारण कोई खराबी या प्रदर्शन में गिरावट न हो। | संगतता संबंधी समस्याओं को रोककर वास्तविक दुनिया के अनुप्रयोगों में सुचारू संचालन सुनिश्चित करता है। |
3.3 पैकेजिंग और भंडारण
वेफर कटिंग के बाद, चिप्स सेमीकंडक्टर निर्माण प्रक्रिया का एक महत्वपूर्ण उत्पाद होते हैं, और उनकी पैकेजिंग और भंडारण चरण भी उतने ही महत्वपूर्ण होते हैं। उचित पैकेजिंग और भंडारण उपाय न केवल परिवहन और भंडारण के दौरान चिप्स की सुरक्षा और स्थिरता सुनिश्चित करने के लिए, बल्कि बाद के उत्पादन, परीक्षण और पैकेजिंग चरणों के लिए मज़बूत समर्थन प्रदान करने के लिए भी आवश्यक हैं।
निरीक्षण और परीक्षण चरणों का सारांश:
वेफर कटिंग के बाद चिप्स के निरीक्षण और परीक्षण के चरणों में दृश्य निरीक्षण, आकार मापन, विद्युत प्रदर्शन परीक्षण, कार्यात्मक परीक्षण, विश्वसनीयता परीक्षण और संगतता परीक्षण सहित कई पहलू शामिल होते हैं। ये चरण आपस में जुड़े और पूरक हैं, जो उत्पाद की गुणवत्ता और विश्वसनीयता सुनिश्चित करने के लिए एक ठोस आधार प्रदान करते हैं। सख्त निरीक्षण और परीक्षण प्रक्रियाओं के माध्यम से, संभावित समस्याओं की पहचान की जा सकती है और उनका शीघ्र समाधान किया जा सकता है, जिससे यह सुनिश्चित होता है कि अंतिम उत्पाद ग्राहकों की आवश्यकताओं और अपेक्षाओं के अनुरूप हो।
पहलू | सामग्री |
पैकेजिंग उपाय | 1.एंटी स्टेटिकपैकेजिंग सामग्री में उत्कृष्ट एंटी-स्टेटिक गुण होने चाहिए ताकि स्थैतिक बिजली से उपकरणों को नुकसान पहुंचने या उनके प्रदर्शन पर असर पड़ने से रोका जा सके। |
2.नमी-प्रूफपैकेजिंग सामग्री में नमी के कारण होने वाले क्षरण और विद्युत प्रदर्शन में गिरावट को रोकने के लिए अच्छी नमी प्रतिरोधकता होनी चाहिए। | |
3.shockproofपैकेजिंग सामग्री को परिवहन के दौरान चिप्स को कंपन और प्रभाव से बचाने के लिए प्रभावी आघात अवशोषण प्रदान करना चाहिए। | |
भंडारण वातावरण | 1.आर्द्रता नियंत्रणअत्यधिक आर्द्रता के कारण होने वाले नमी अवशोषण और क्षरण या कम आर्द्रता के कारण होने वाली स्थैतिक समस्याओं को रोकने के लिए उचित सीमा के भीतर आर्द्रता को सख्ती से नियंत्रित करें। |
2.स्वच्छताधूल और अशुद्धियों से चिप्स के संदूषण से बचने के लिए स्वच्छ भंडारण वातावरण बनाए रखें। | |
3.तापमान नियंत्रण: अत्यधिक गर्मी या कम तापमान के कारण होने वाली संघनन समस्याओं के कारण त्वरित उम्र बढ़ने को रोकने के लिए एक उचित तापमान सीमा निर्धारित करें और तापमान स्थिरता बनाए रखें। | |
नियमित निरीक्षण | समय-समय पर संभावित समस्याओं की पहचान करने और उनका समाधान करने के लिए दृश्य निरीक्षण, आकार माप और विद्युत प्रदर्शन परीक्षणों का उपयोग करके संग्रहीत चिप्स का नियमित रूप से निरीक्षण और मूल्यांकन करें। भंडारण समय और स्थितियों के आधार पर, चिप्स के उपयोग की योजना बनाएं ताकि यह सुनिश्चित हो सके कि उनका उपयोग इष्टतम स्थिति में किया जाए। |
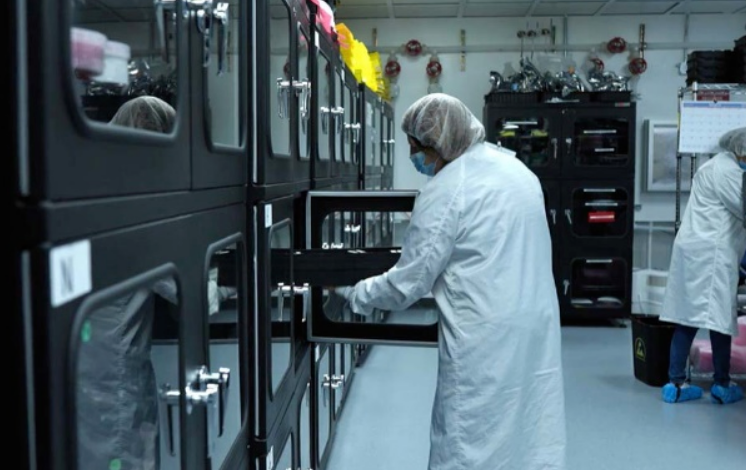
वेफर डाइसिंग प्रक्रिया के दौरान माइक्रोक्रैक और क्षति का मुद्दा सेमीकंडक्टर विनिर्माण में एक महत्वपूर्ण चुनौती है। कटिंग तनाव इस घटना का प्राथमिक कारण है, क्योंकि यह वेफर सतह पर छोटी दरारें और क्षति पैदा करता है, जिससे विनिर्माण लागत बढ़ जाती है और उत्पाद की गुणवत्ता में कमी आती है।
इस चुनौती का समाधान करने के लिए, काटने के तनाव को कम करना और अनुकूलित काटने की तकनीकों, उपकरणों और परिस्थितियों को लागू करना बेहद ज़रूरी है। ब्लेड की सामग्री, काटने की गति, दबाव और शीतलन विधियों जैसे कारकों पर सावधानीपूर्वक ध्यान देने से सूक्ष्म दरारों के निर्माण को कम करने और प्रक्रिया की समग्र उत्पादकता में सुधार करने में मदद मिल सकती है। इसके अतिरिक्त, लेज़र डाइसिंग जैसी अधिक उन्नत काटने की तकनीकों पर चल रहे शोध इन समस्याओं को और कम करने के तरीके खोज रहे हैं।
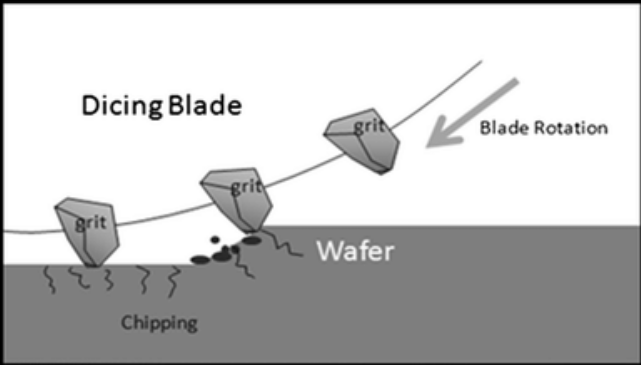
एक नाज़ुक पदार्थ होने के कारण, वेफ़र्स यांत्रिक, तापीय या रासायनिक दबाव के कारण आंतरिक संरचनात्मक परिवर्तनों से ग्रस्त हो सकते हैं, जिससे सूक्ष्म दरारें बन सकती हैं। हालाँकि ये दरारें तुरंत दिखाई नहीं देतीं, लेकिन निर्माण प्रक्रिया के दौरान ये फैल सकती हैं और अधिक गंभीर क्षति पहुँचा सकती हैं। यह समस्या बाद के पैकेजिंग और परीक्षण चरणों के दौरान विशेष रूप से समस्याग्रस्त हो जाती है, जहाँ तापमान में उतार-चढ़ाव और अतिरिक्त यांत्रिक दबाव इन सूक्ष्म दरारों को दृश्यमान दरारों में बदल सकते हैं, जिससे संभावित रूप से चिप विफलता हो सकती है।
इस जोखिम को कम करने के लिए, काटने की गति, दबाव और तापमान जैसे मापदंडों को अनुकूलित करके काटने की प्रक्रिया को सावधानीपूर्वक नियंत्रित करना आवश्यक है। लेज़र डाइसिंग जैसी कम आक्रामक काटने की विधियों का उपयोग करने से वेफर पर यांत्रिक तनाव कम हो सकता है और सूक्ष्म दरारें न्यूनतम हो सकती हैं। इसके अतिरिक्त, वेफर डाइसिंग प्रक्रिया के दौरान इन्फ्रारेड स्कैनिंग या एक्स-रे इमेजिंग जैसी उन्नत निरीक्षण विधियों को लागू करने से इन प्रारंभिक चरण की दरारों का पता लगाने में मदद मिल सकती है, इससे पहले कि वे और अधिक नुकसान पहुँचाएँ।
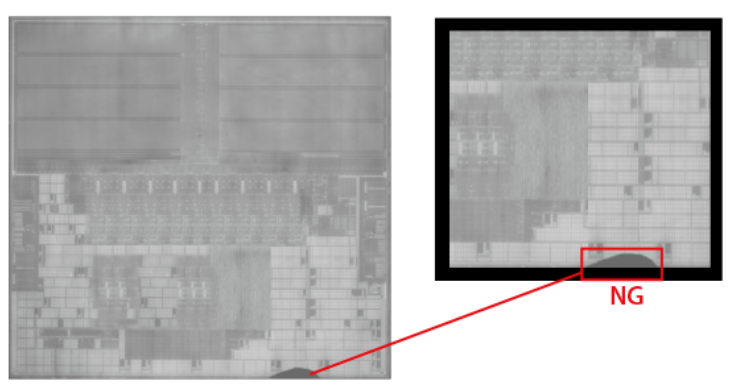
वेफर की सतह को होने वाली क्षति, डाइसिंग प्रक्रिया में एक महत्वपूर्ण चिंता का विषय है, क्योंकि इसका चिप के प्रदर्शन और विश्वसनीयता पर सीधा प्रभाव पड़ सकता है। यह क्षति काटने वाले औज़ारों के अनुचित उपयोग, गलत कटिंग मापदंडों, या वेफर में निहित भौतिक दोषों के कारण हो सकती है। कारण चाहे जो भी हो, इन क्षतियों से सर्किट के विद्युत प्रतिरोध या धारिता में परिवर्तन हो सकता है, जिससे समग्र प्रदर्शन प्रभावित हो सकता है।
इन मुद्दों के समाधान के लिए दो प्रमुख रणनीतियों पर विचार किया जा रहा है:
1.काटने के उपकरण और मापदंडों का अनुकूलन: तेज ब्लेड का उपयोग करके, काटने की गति को समायोजित करके, और काटने की गहराई को संशोधित करके, काटने की प्रक्रिया के दौरान तनाव की एकाग्रता को कम किया जा सकता है, जिससे क्षति की संभावना कम हो जाती है।
2.नई कटिंग तकनीकों की खोजलेजर कटिंग और प्लाज़्मा कटिंग जैसी उन्नत तकनीकें बेहतर परिशुद्धता प्रदान करती हैं, जबकि वेफ़र पर होने वाले नुकसान के स्तर को संभावित रूप से कम करती हैं। वेफ़र पर थर्मल और मैकेनिकल तनाव को कम करते हुए उच्च कटिंग परिशुद्धता प्राप्त करने के तरीके खोजने के लिए इन तकनीकों का अध्ययन किया जा रहा है।
तापीय प्रभाव क्षेत्र और प्रदर्शन पर इसका प्रभाव
लेजर और प्लाज़्मा कटिंग जैसी थर्मल कटिंग प्रक्रियाओं में, उच्च तापमान अनिवार्य रूप से वेफ़र की सतह पर एक थर्मल प्रभाव क्षेत्र बनाता है। यह क्षेत्र, जहाँ तापमान प्रवणता महत्वपूर्ण है, सामग्री के गुणों को बदल सकता है, जिससे चिप का अंतिम प्रदर्शन प्रभावित होता है।
थर्मल प्रभावित क्षेत्र (TAZ) का प्रभाव:
क्रिस्टल संरचना में परिवर्तन: उच्च तापमान पर, वेफर सामग्री के भीतर परमाणु पुनर्व्यवस्थित हो सकते हैं, जिससे क्रिस्टल संरचना में विकृति हो सकती है। यह विकृति सामग्री को कमजोर करती है, इसकी यांत्रिक शक्ति और स्थिरता को कम करती है, जिससे उपयोग के दौरान चिप के खराब होने का जोखिम बढ़ जाता है।
विद्युत गुणों में परिवर्तनउच्च तापमान अर्धचालक पदार्थों में वाहक सांद्रता और गतिशीलता को बदल सकता है, जिससे चिप की विद्युत चालकता और वर्तमान संचरण दक्षता प्रभावित होती है। इन परिवर्तनों से चिप के प्रदर्शन में गिरावट आ सकती है, जिससे यह अपने इच्छित उद्देश्य के लिए अनुपयुक्त हो सकता है।
इन प्रभावों को कम करने के लिए, काटने के दौरान तापमान को नियंत्रित करना, काटने के मापदंडों को अनुकूलित करना, तथा कूलिंग जेट या प्रसंस्करण के बाद उपचार जैसे तरीकों की खोज करना, तापीय प्रभाव की सीमा को कम करने और सामग्री की अखंडता को बनाए रखने के लिए आवश्यक रणनीतियां हैं।
कुल मिलाकर, माइक्रोक्रैक और थर्मल इम्पैक्ट ज़ोन दोनों ही वेफर डाइसिंग तकनीक में महत्वपूर्ण चुनौतियाँ हैं। सेमीकंडक्टर उत्पादों की गुणवत्ता में सुधार और उनकी बाज़ार प्रतिस्पर्धात्मकता को बढ़ाने के लिए तकनीकी प्रगति और गुणवत्ता नियंत्रण उपायों के साथ-साथ निरंतर शोध आवश्यक होगा।
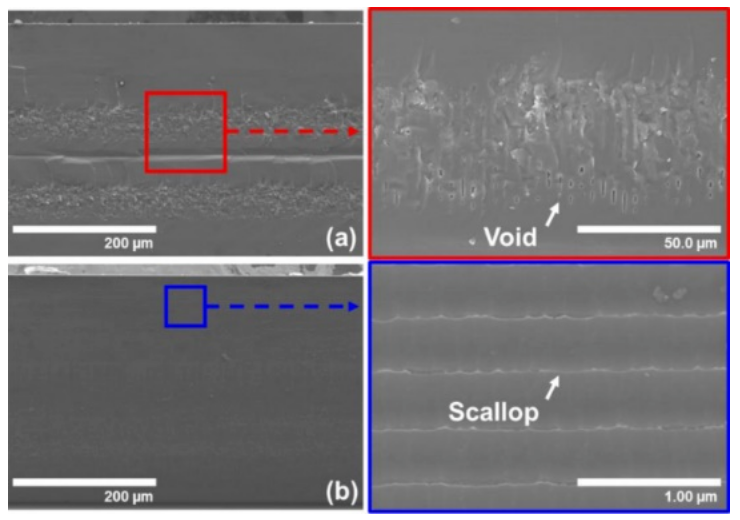
तापीय प्रभाव क्षेत्र को नियंत्रित करने के उपाय:
काटने की प्रक्रिया के मापदंडों का अनुकूलनकटिंग की गति और शक्ति को कम करने से थर्मल इम्पैक्ट ज़ोन (TAZ) के आकार को प्रभावी ढंग से कम किया जा सकता है। इससे कटिंग प्रक्रिया के दौरान उत्पन्न होने वाली गर्मी की मात्रा को नियंत्रित करने में मदद मिलती है, जो सीधे वेफर के भौतिक गुणों को प्रभावित करती है।
उन्नत शीतलन प्रौद्योगिकियांद्रव नाइट्रोजन शीतलन और सूक्ष्म-द्रवीय शीतलन जैसी तकनीकों का उपयोग तापीय प्रभाव क्षेत्र की सीमा को महत्वपूर्ण रूप से सीमित कर सकता है। ये शीतलन विधियाँ ऊष्मा को अधिक कुशलता से नष्ट करने में मदद करती हैं, जिससे वेफर के भौतिक गुणों का संरक्षण होता है और तापीय क्षति न्यूनतम होती है।
सामग्री चयनशोधकर्ता कार्बन नैनोट्यूब और ग्रेफीन जैसी नई सामग्रियों की खोज कर रहे हैं, जिनमें उत्कृष्ट तापीय चालकता और यांत्रिक शक्ति होती है। ये सामग्रियाँ तापीय प्रभाव क्षेत्र को कम कर सकती हैं और साथ ही चिप्स के समग्र प्रदर्शन में सुधार कर सकती हैं।
संक्षेप में, हालाँकि थर्मल इम्पैक्ट ज़ोन थर्मल कटिंग तकनीकों का एक अपरिहार्य परिणाम है, इसे अनुकूलित प्रसंस्करण तकनीकों और सामग्री चयन के माध्यम से प्रभावी ढंग से नियंत्रित किया जा सकता है। भविष्य के शोध संभवतः अधिक कुशल और सटीक वेफर डाइसिंग प्राप्त करने के लिए थर्मल कटिंग प्रक्रियाओं को बेहतर बनाने और स्वचालित करने पर केंद्रित होंगे।

संतुलन रणनीति:
वेफर डाइसिंग तकनीक में वेफर उपज और उत्पादन क्षमता के बीच इष्टतम संतुलन हासिल करना एक सतत चुनौती है। निर्माताओं को एक तर्कसंगत उत्पादन रणनीति और प्रक्रिया मानदंड विकसित करने के लिए बाजार की मांग, उत्पादन लागत और उत्पाद की गुणवत्ता जैसे कई कारकों पर विचार करना होगा। साथ ही, उन्नत कटिंग उपकरणों का उपयोग, ऑपरेटर कौशल में सुधार और कच्चे माल की गुणवत्ता नियंत्रण को बढ़ाना, उत्पादन क्षमता बढ़ाते हुए उपज को बनाए रखने या यहाँ तक कि उसे बेहतर बनाने के लिए आवश्यक है।
भविष्य की चुनौतियाँ और अवसर:
सेमीकंडक्टर तकनीक की प्रगति के साथ, वेफर कटिंग नई चुनौतियों और अवसरों का सामना कर रही है। जैसे-जैसे चिप का आकार छोटा होता जा रहा है और एकीकरण बढ़ रहा है, कटिंग की सटीकता और गुणवत्ता की माँगें काफ़ी बढ़ रही हैं। साथ ही, उभरती हुई तकनीकें वेफर कटिंग तकनीकों के विकास के लिए नए विचार प्रदान करती हैं। निर्माताओं को बाज़ार की गतिशीलता और तकनीकी रुझानों के प्रति सजग रहना चाहिए, और बाज़ार में होने वाले बदलावों और तकनीकी माँगों के अनुरूप उत्पादन रणनीतियों और प्रक्रिया मापदंडों को लगातार समायोजित और अनुकूलित करना चाहिए।
निष्कर्षतः, बाजार की मांग, उत्पादन लागत और उत्पाद की गुणवत्ता के विचारों को एकीकृत करके, तथा उन्नत उपकरण और प्रौद्योगिकी को लागू करके, ऑपरेटर कौशल को बढ़ाकर और कच्चे माल के नियंत्रण को मजबूत करके, निर्माता वेफर डाइसिंग के दौरान वेफर उपज और उत्पादन दक्षता के बीच सर्वोत्तम संतुलन प्राप्त कर सकते हैं, जिससे कुशल और उच्च गुणवत्ता वाले अर्धचालक उत्पाद का उत्पादन हो सकता है।
भविष्य का दृष्टिकोण:
तेज़ी से तकनीकी प्रगति के साथ, सेमीकंडक्टर तकनीक अभूतपूर्व गति से आगे बढ़ रही है। सेमीकंडक्टर निर्माण में एक महत्वपूर्ण कदम के रूप में, वेफर कटिंग तकनीक रोमांचक नए विकास के लिए तैयार है। भविष्य में, वेफर कटिंग तकनीक से सटीकता, दक्षता और लागत में उल्लेखनीय सुधार होने की उम्मीद है, जो सेमीकंडक्टर उद्योग के निरंतर विकास में नई ऊर्जा का संचार करेगा।
बढ़ती परिशुद्धता:
उच्च परिशुद्धता की खोज में, वेफर कटिंग तकनीक मौजूदा प्रक्रियाओं की सीमाओं को निरंतर आगे बढ़ाएगी। कटिंग प्रक्रिया के भौतिक और रासायनिक तंत्रों का गहन अध्ययन करके और कटिंग मापदंडों को सटीक रूप से नियंत्रित करके, बढ़ती हुई जटिल सर्किट डिज़ाइन आवश्यकताओं को पूरा करने के लिए बेहतर कटिंग परिणाम प्राप्त किए जा सकेंगे। इसके अतिरिक्त, नई सामग्रियों और कटिंग विधियों की खोज से उपज और गुणवत्ता में उल्लेखनीय सुधार होगा।
दक्षता बढ़ाना:
नए वेफर कटिंग उपकरण स्मार्ट और स्वचालित डिज़ाइन पर केंद्रित होंगे। उन्नत नियंत्रण प्रणालियों और एल्गोरिदम की शुरूआत से उपकरण विभिन्न सामग्रियों और डिज़ाइन आवश्यकताओं के अनुसार कटिंग मापदंडों को स्वचालित रूप से समायोजित कर सकेंगे, जिससे उत्पादन दक्षता में उल्लेखनीय सुधार होगा। मल्टी-वेफर कटिंग तकनीक और रैपिड ब्लेड रिप्लेसमेंट सिस्टम जैसे नवाचार दक्षता बढ़ाने में महत्वपूर्ण भूमिका निभाएंगे।
लागत कम करना:
वेफर कटिंग तकनीक के विकास के लिए लागत में कमी एक महत्वपूर्ण दिशा है। जैसे-जैसे नई सामग्री और कटिंग विधियाँ विकसित होंगी, उपकरणों की लागत और रखरखाव व्यय पर प्रभावी नियंत्रण की उम्मीद है। इसके अतिरिक्त, उत्पादन प्रक्रियाओं को अनुकूलित करने और स्क्रैप दरों को कम करने से विनिर्माण के दौरान अपशिष्ट में और कमी आएगी, जिससे समग्र उत्पादन लागत में कमी आएगी।
स्मार्ट विनिर्माण और IoT:
स्मार्ट मैन्युफैक्चरिंग और इंटरनेट ऑफ थिंग्स (IoT) तकनीकों का एकीकरण वेफर कटिंग तकनीक में क्रांतिकारी बदलाव लाएगा। उपकरणों के बीच इंटरकनेक्टिविटी और डेटा शेयरिंग के माध्यम से, उत्पादन प्रक्रिया के हर चरण की वास्तविक समय में निगरानी और अनुकूलन किया जा सकता है। इससे न केवल उत्पादन क्षमता और उत्पाद की गुणवत्ता में सुधार होता है, बल्कि कंपनियों को बाज़ार का अधिक सटीक पूर्वानुमान और निर्णय लेने में सहायता भी मिलती है।
भविष्य में, वेफर कटिंग तकनीक सटीकता, दक्षता और लागत के मामले में उल्लेखनीय प्रगति करेगी। ये प्रगति सेमीकंडक्टर उद्योग के निरंतर विकास को गति प्रदान करेगी और मानव समाज के लिए और अधिक तकनीकी नवाचार और सुविधाएँ लाएगी।
पोस्ट करने का समय: नवम्बर-19-2024